Ice Maker and Ice Machine Services
NEAR Jackson, MS
At Davis Refrigeration & Electrical, one of our main focuses is Ice Machine repair and replacement. When you run a business that needs ice, whether for soft drinks for customers, or your own purposes, it’s important to have your ice machine regularly cleaned.
The icemaker is an important part of any restaurant. When it’s on the fritz, you’re sure to get many customer complaints. Not only that, but a broken icemaker could also cause major health issues. That’s why it’s important to address any icemaker problems as soon as possible. Even the smallest problems could cause big problems down the line.
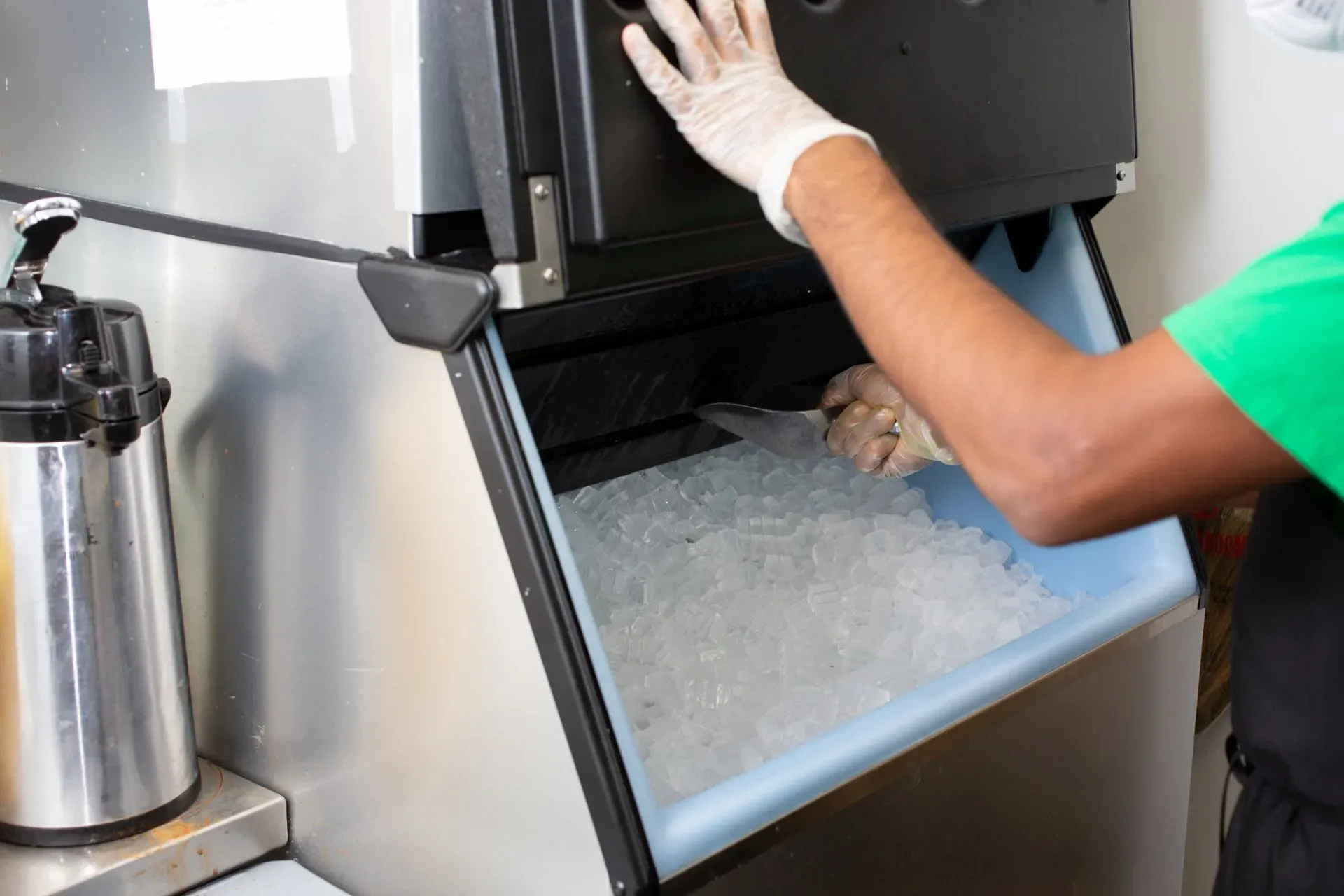
Common Signs Your Ice Machine Needs Service
Our team has nearly 70 years of combined experience in the field of commercial refrigeration technology. We offer maintenance plans where our professional team will check water filtration system to ensure your ice is sanitary on a regular basis. This way, you keep your customers happy and healthy!
- Low Ice Production
- Cloudy Ice
- Small Ice Cube Size
- Sliminess
- Leaking
- Motor won’t shut off
- Ice or Frost Build-up
FAQS about Ice machines & Ice makerS
ICE MACHINE MAINTENANCE PLAN
Protect your investment! Keeping your ice equipment running efficiently and properly sanitized requires regular scheduled maintenance; to prevent breakdown and maintain efficiency. Our inspections and checks include the following:
- Clean and sanitize the water system.
- Volts-amps on compressors
- Volts-amps on condenser fans
- Check inlet water valve screens
- Volts-amps
- Connections
- High limit & safeties
- Overall cleanliness
- Clean air filters on air-cooled models.
- Safeties
- Check external filter system and change cartridges as needed, IF APPLICABLE
- Lubricate shafts & bearings-condenser fans
- Conduct bearing and auger inspection on extruded ice makers
- Visual inspection of components
- Visual check for leaks
- Condenser coil
- Suction pressure cutout
- Suction pressure & discharge pressure
- Refrigeration charge, hi-low superheat
- Draft fan for dirt & rust
* All contracts include a chemical cleaning of your evaporator & condenser coils.
Priority Emergency Service - Should you have a breakdown, our own dispatched service technicians will respond to your call as a priority service call. We service our Commercial Service Policy customers first.
Discount on Repairs - When you become a Davis Refrigeration Commercial Service Policy holder you are entitled to a 15% discount on all parts and equipment installed while under contract.
To schedule ice machine maintenance, give our team a call today: